Rotary Actuator
Contents
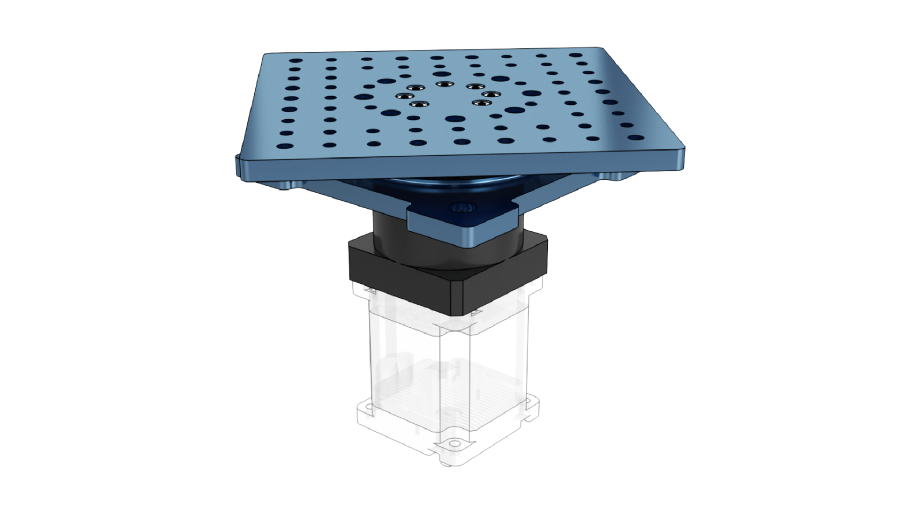
Overview
The assembly of the Rotary Actuator v2 consists of a concealed 10:1 flanged gearbox between two Vention compatible plates. The bottom mounting allows for any combination of Vention’s NEMA 34 stepper servo motors. With a 10:1 reduction present on the actuator, multiple levels of torque can be achieved. The bottom plate also features mounting holes that interface perfectly with Vention extrusions. The top plate features multiple countersunk and threaded holes for all your mounting purposes.
This datasheet provides technical specifications for Vention’s Rotary Actuator V2. For details on Vention’s Rotary Actuator V1, refer to the ‘Documentation for Previous Product Versions’ section at the bottom of this page.
Applications
There are several application for 4th Axis Palletizer or a Rotary Inspection Station for Universal Robots.
Technical Specifications
Maximum Torque Combinations
Max Torque - Motor and Actuator [Nm] | |
MO-SM-011-0000 | 80.0 |
MO-SM-012-0000 | 45.0 |
MO-SM-013-0000 | 20.0 |
The below figure gives the performance of the rotary actuator torque vs speed with all of Vention’s stepper motor combinations driven by MachineMotion 2.
Note: These performance curves are made with our motors and controller at steady state conditions. Using others motors or controllers will have different behavior therefore performance and reliability cannot be guaranteed.
Specifications
Nominal Backlash [arcmin] | ≤13.6 |
Nominal Tilting Play [degrees] | ±0.113 |
Maximum Rotational Velocity [RPM] | 225 (dictated by motor maximum) |
Radial Capacity (Static)*[N] | 1100 |
Radial Capacity (Dynamic) [N] | 235 |
Axial Capacity (Static)*[N] | 2850 |
Axial Capacity (Dynamic) [N] | 2850 |
Maximum Tilting Moment (Static)*[Nm] | 275 |
Maximum Tilting Moment (Dynamic) [Nm] | 0 |
Motor Compatibility | NEMA 34, 14mm shaft MO-SM-011-0000, MO-SM-012-0000, MO-SM-013-0000 |
Note*: Assumes low rpm operation (<10 rpm) and only one static force present. For combined loading reach out to application engineering.
Maximum Inertia
Dimensionally large or heavy assemblies have a lot inertia. Large amounts of driven inertia on the output of the actuator will cause it to function poorly. Generally it is recommended to stay below 20 kg*m² for this actuator. Going above this value decreases the performance of the actuator in two ways. First large oscillations will start to occur near the inputted desired position. Secondly, the actuator will struggle to accelerate and decelerate the load. When large inertias are unavoidable, consult this chart to determine maximum speed.
Assembly
Motor Mounting
The Rotary Actuator is compatible with all of Vention’s NEMA 34 Stepper Servo motors. The Rotary Actuator is not compatible with any gearboxes.
Notes:
- When installing motors, apply a small amount of grease to the motor shaft so that it is lightly coated. This will reduce the possibility of fretting corrosion occurring during operation, making future removal easier.
- Moreover, do not use excessive force (hammering, prying or using screws to “push” the motor) to install the motor.
- Be sure to tighten the two clamping screws on the input collar behind the plastic covers.
Mounting Sensors
You can add home and end sensors to a rotary actuator, and they will work the same way as home and end sensors on a linear actuator.
A home position sensor enables repeatable motion: it provides a reference point to which the actuator can “zero.” Adding both home and end position sensors means that in addition to enabling repeatable motion, you can also limit the actuator’s travel.
The home and position sensors are both inductive proximity sensors (CE-SN-004-0003). They are each mounted to a block (MO-RM-002-0007), which is itself mounted to the rotary actuator with two M6 x 35-mm screws (HW-FN-005-1035).
The sensors are activated when they approach a trigger. Two triggers—one for each sensor—are typically mounted to the underside of the top plate. Each trigger is mounted through a slot, which allows its position to be fine-tuned, with two M4 x 8-mm screws (HW-FN-010-0008).