2 cobots freeing up 10 employees per production shift
Niederrhein Automation introduced two cobots to ensure production scalability and consistency without additional headcount.
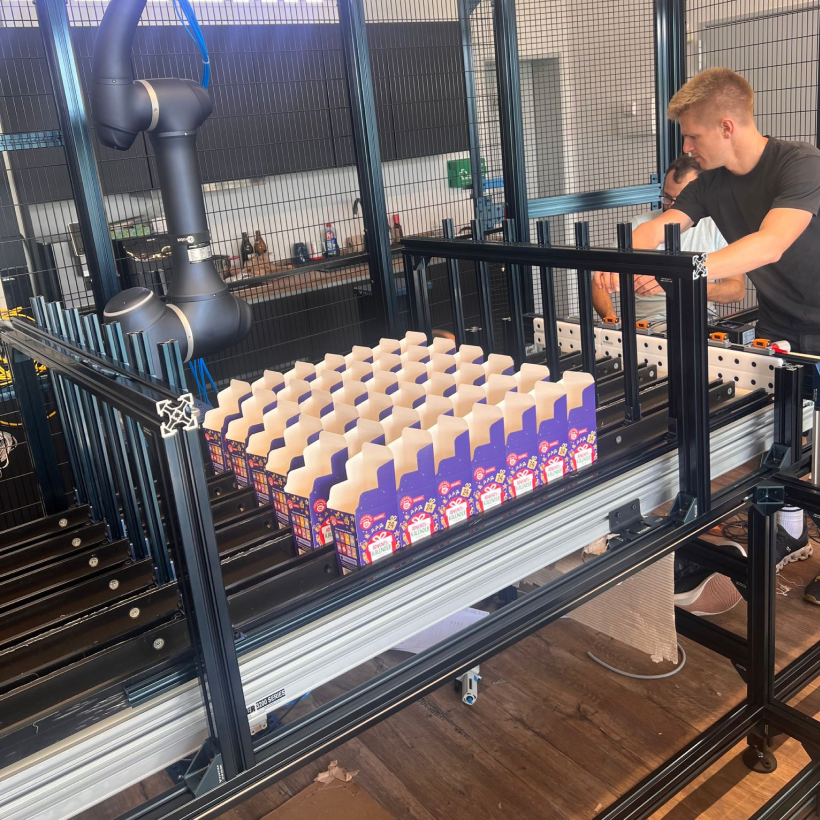
Geschichte Highlights
The number of filled cartons per shift increased from 800 to 1200.
8-10 employees per production shift were reallocated to more value-added tasks.
2 collaborative robots serving 2 production lines.
The technology was seamlessly integrated into existing equipment thanks to Vention’s digital twin capabilities.
Das Problem
Labor shortages continue to be a significant hurdle for manufacturers looking to maintain or increase their productivity. This is the main reason why Niederrhein Automation’s customer wanted to automate their most repetitive task: tea bag packaging.
The new automated system needed to tap into the existing production line. With a tight deadline, project coordination was critical and one of the main reasons why Niederrhein Automation partnered with Vention for this project.
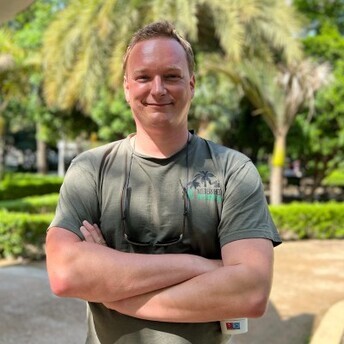
"Working with Vention makes our lives simpler and our customers happier. This project could not have been realized without Vention’s quick quoting, fast lead times, and simple online tools."
Das Projekt
With Vention’s digital twin capabilities in MachineBuilder, a solution was created that fully automates the tea bag packing process for this food & beverage manufacturer. The resulting solution was two Doosan cobots equipped with custom grippers and a 14-meter-long conveyor belt system.
The hardware from Vention was delivered swiftly, allowing Niederrhein Automation to program the robot cell and integrate it into the existing process within the client’s timeframe.
Die Ergebnisse
Niederrhein Automation successfully deployed this custom machine with the help of Vention, eliminating the need for manual tasks by employees and significantly increasing packaging efficiency. These cobots have reallocated 8-10 employees per production shift who used to manually fill over 800 cartons during one shift.
The end customer is highly satisfied with the implementation of the automation solution. Additionally, the consistent quality and the creation of a second production shift as a ‘ghost shift’ represents a significant improvement and benefit for the company. Employees are now assigned to more profitable processes within the company.
Projekt Spezifikationen
Learn more about Niederrhein Automation
Explore Niederrhein Automation capabilities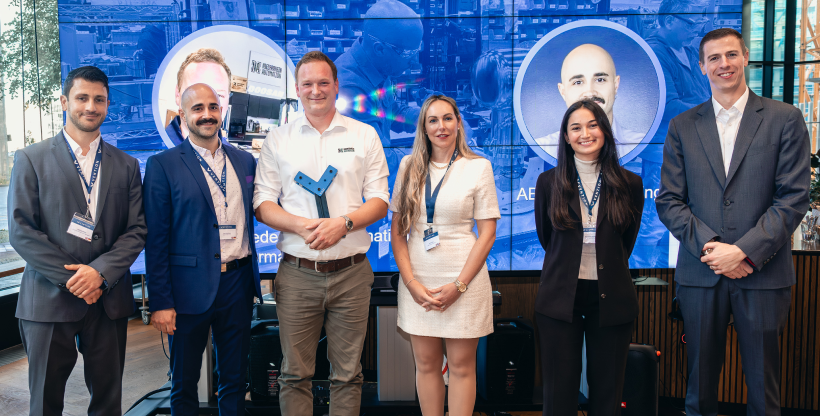