Dual pick-and-place system for inspection and packaging
Ora Graphene increased its production volumes 4x without incurring any additional labor costs, thanks to automation.
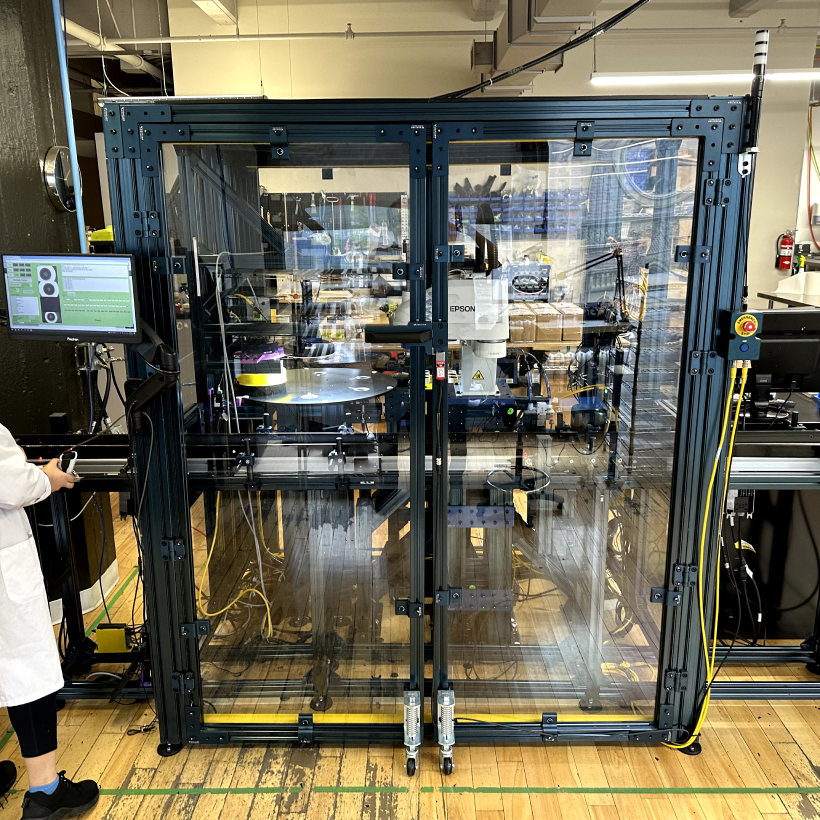
Story Highlights
Automating manual processes resulted in a 4x increase in production volume.
Two pick-and-place machines were fully deployed in under 2 weeks to start earning ROI faster.
Return on investment realized within 7 months, leading to future automation opportunities.
Employees were reallocated from manual processes to more value-added tasks.
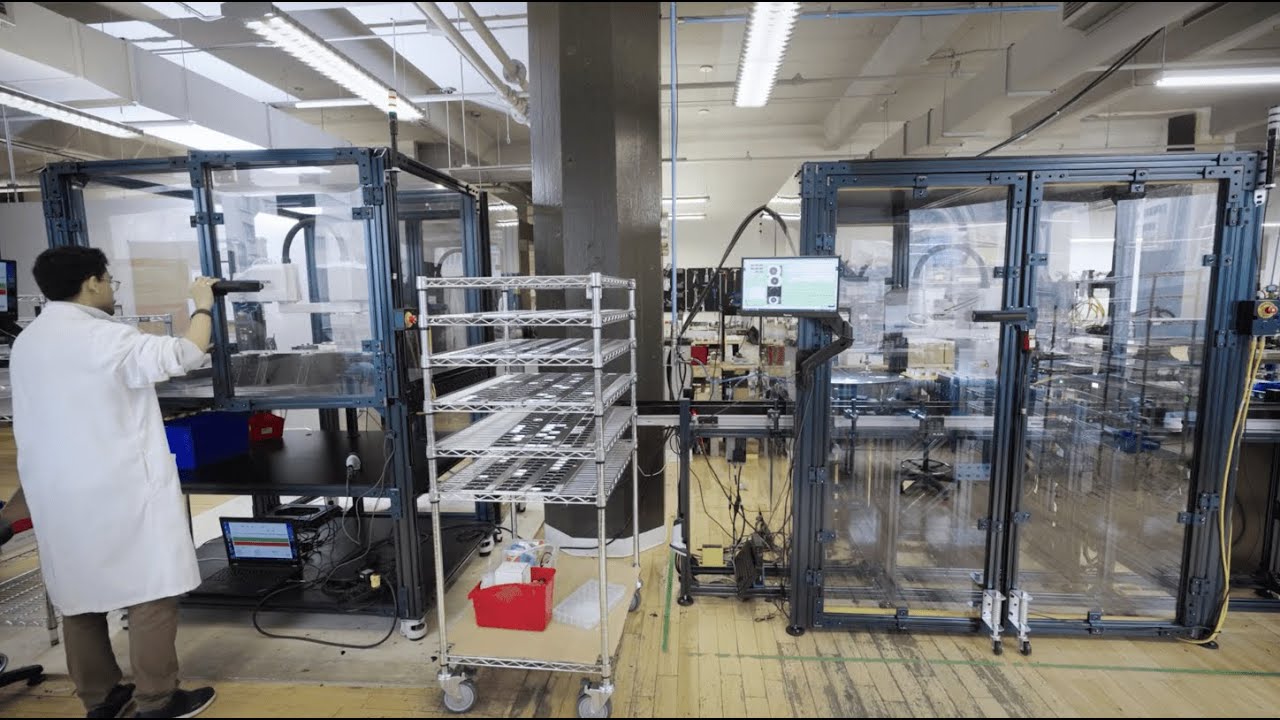
The Problem
Ora Graphene is bringing the world’s first graphene-based audio components to market. The product delivers an unparalleled listening experience, and its headphones are especially popular among gamers.
Manufacturing their products is time-consuming, labor-intensive, and all done in-house. It requires manual inspection of each sample produced and then processing into custom packaging. This led to a slowdown in Ora’s manufacturing times and limited their ability to scale production as demand for the product increased.
Seeing an opportunity to improve production capacity, profit margins, and quality through automation, Ora began researching industrial automation companies to partner with to bring their dreams to reality.
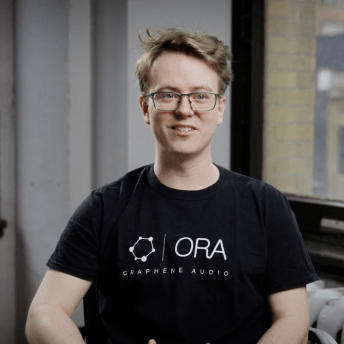
"The main reason we went with Vention is they were so fast to respond. Our timelines were very tight, and we had already received prototype designs before even hearing back from other companies."
The Project
Ora chose to partner with Vention because of the fast response times and thorough prototyping. Together, Vention and Ora collaboratively created an automated solution to meet demand while delivering a strong return on investment. The resulting solution involved two pick-and-place machines featuring a Vention vacuum and conveyor system, a MachineMotion controller with a pendant, and an Epson T6 robot.
The first machine is a mass pick-and-place system, which weighs each individual sample and returns them to a tray for further processing. The second machine is a pick-and-place packaging system that picks up samples, places them on a rotary table, takes pictures, and then packages them in custom packaging.
The machines were programmed in-house using Epson Programming (RC+). Vention supported in connecting the actuators with the robot so commands could be completed through Epson programming, rather than creating an additional interface.
Introducing these two solutions to automate the manual inspection and packaging of samples has allowed Ora to reallocate their workforce from repetitive and labor-intensive tasks to more high-value tasks.
The Results
What was previously a manual process, where employees had to individually verify every single sample, is now an automated process, freeing up employees for more high-value tasks.
With the introduction of the two pick-and-place machines, Ora improved its manufacturing speed and quality, quadrupling production capacity. Now, they are able to reach the scale needed to fulfill demand, resulting in increased profit margins and a return on investment of 7 to 10 months.
“Vention has been incredible in helping us automate [our] processes,” says Eric Gaskell, VP Product. “It’s sped up our manufacturing time and reduced our cycle time and labor costs so we can produce high-quality parts, and improve our quality to our customers.”
Project Specs
Learn more about pick-and-place robots
Discover the Vention difference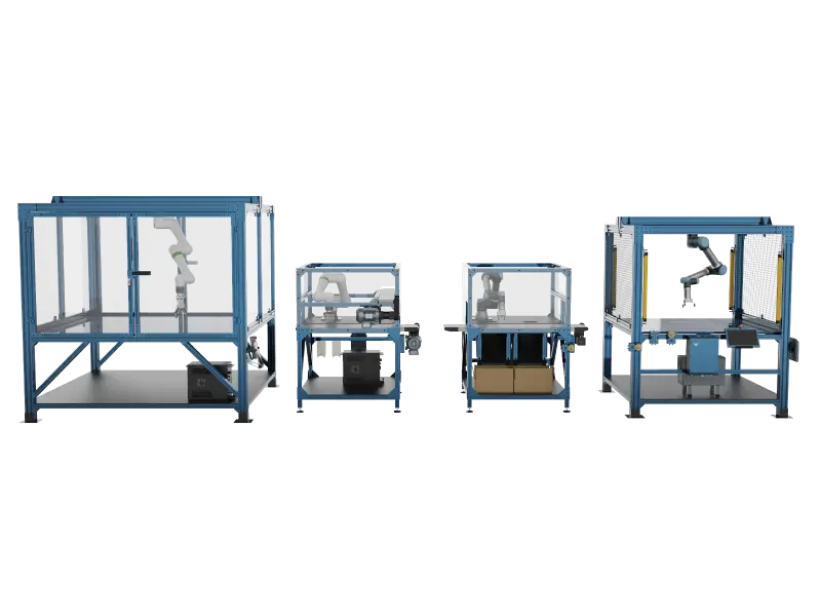