Automating machine tending for lights-out production
FANUC CRX machine tending cell to complete repetitive and manual work, repurposing workers to higher-value tasks and achieving a greater return on investment.
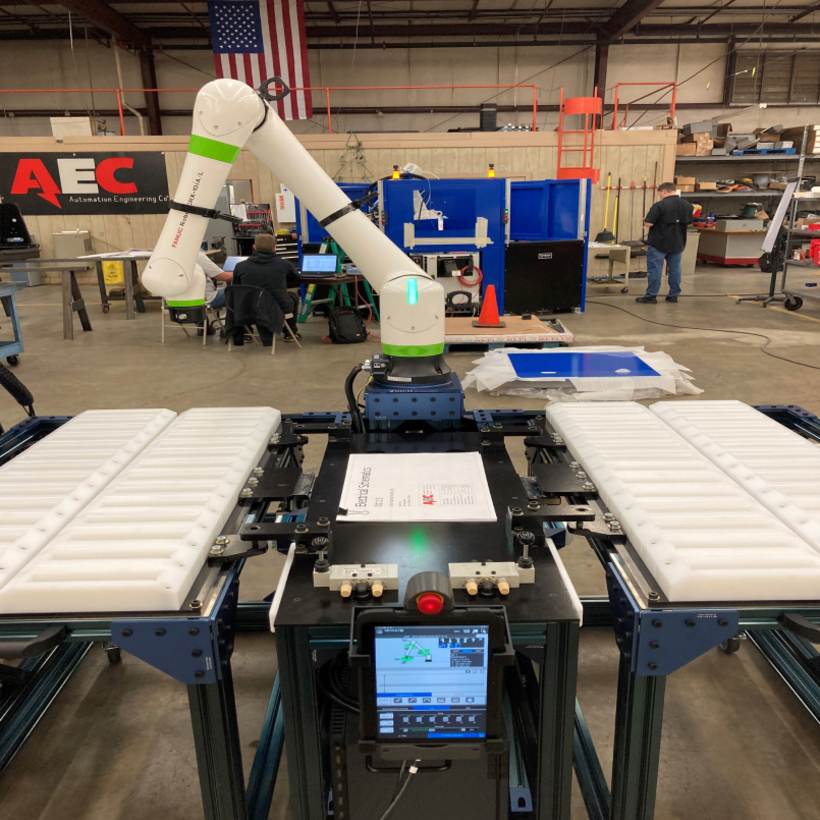
Story Highlights
Gained the ability to run multiple-part families with minimal changeover.
Reallocated FTEs to value-added tasks amid ongoing labor shortage.
Achieved fast return on investment with 20 hours of lights-out production.
Improved safety by eliminating redundant operator tasks such as lifting heavy parts.
The Problem
Automation Engineering Company (AEC) is a Vention Automation Partner and a leading machine builder and automation integrator based in the U.S. Amidst the COVID-19 pandemic, their client faced challenges in maintaining output due to labor shortages.
They approached AEC to create a machine tending solution for coordinate measuring machine (CMM) inspection and part marking. This solution required integrating multiple parts into a robot cell. Additionally, the specialty cast parts had drastic parting lines and variations from one part to another.
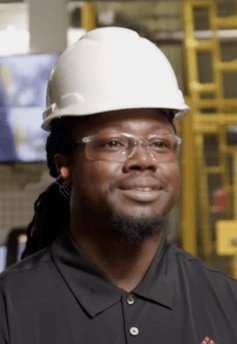
"Filling in labor shortages while offering high-quality, consistent outputs has been challenging since the pandemic. AEC's machine tending solution filled that void while providing the flexibility to run multiple part families with minimal changeover and no robot or programming background required."
The Project
AEC created a custom machine tending solution to meet their client’s unique needs. They began with a FANUC CRX10ia/L robot arm and integrated it into a Vention Robot 7th Axis. The solution extended the robot arm’s reach, enabling it to access all required processes, including inbound dunnage carts, multiple machine tools, a CMM, part marking, and outbound carts.
The parts are picked from the inbound cart by a double end-of-arm tool (EOAT). They are then placed into the machine tool utilizing force feedback and compliance features, transferred to a CMM, followed by part marking, and finally returned to the position from which they were picked on the cart. The CMM automatically sends offsets to the CNC to minimize operator interventions and enable the customer to run lights out.
The Results
AEC was faced with a complex project but devised an innovative solution aided by Vention’s intuitive software and modular hardware. The machine tending solution operates lights out for 20 hours, enabling employees to focus on more value-added tasks and fostering increased production rates without sacrificing quality. After 18 months of operation, the client met the targeted return on investment.
Project Specs
Discover Machine Tending Robots
Learn more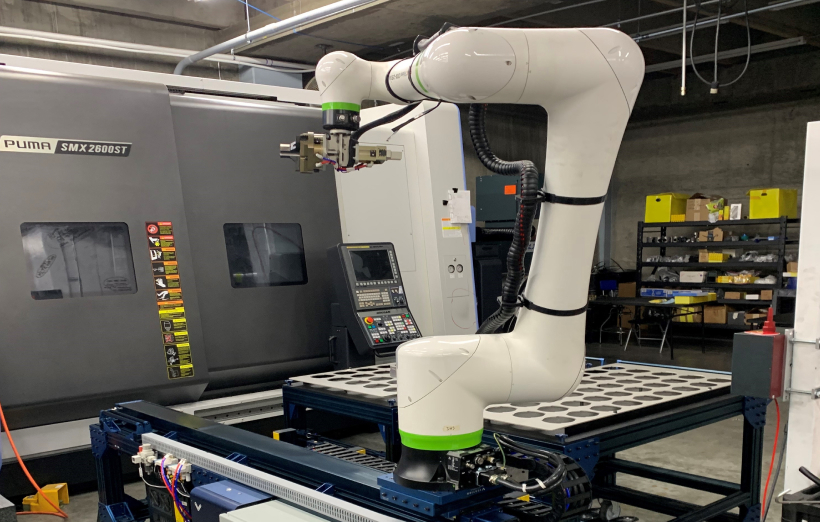