Improving Quoting Speed & Simplifying Sourcing for a Vention Automation Partner
Discover how AE Sewing Machines leveraged Vention's Manufacturing Automation Platform (MAP) to complete projects faster and more cost-effectively.
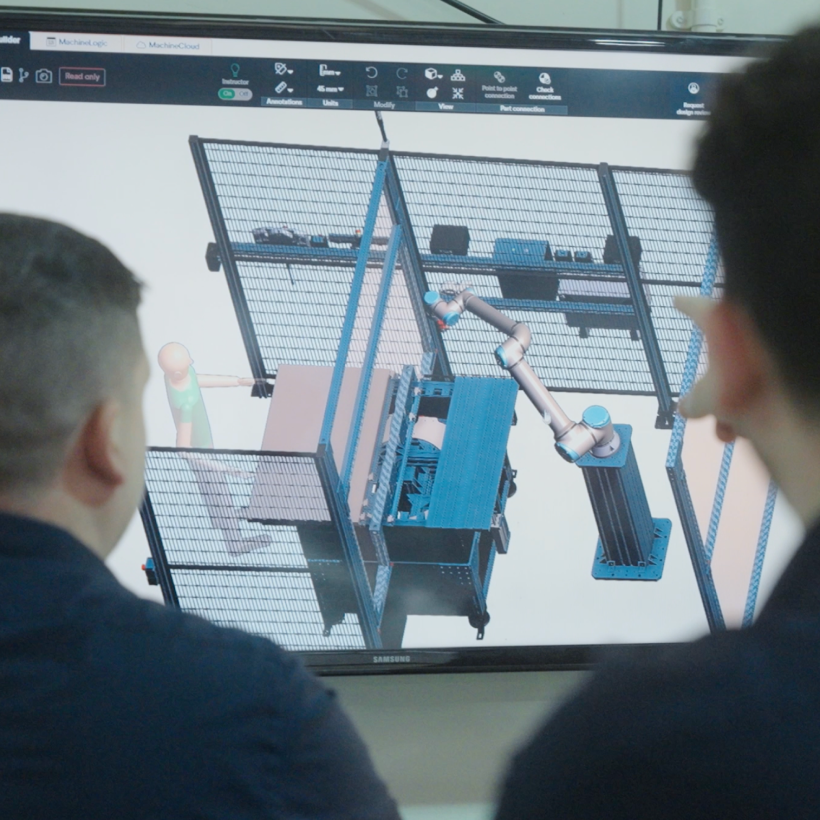
Story Highlights
Streamlined Quoting with Vention’s Platform
AE Sewing Machines used Vention’s tools to provide customers with ROI data early in the process, offering same-day quotes.
Efficient Concept Visualization
Vention’s platform enabled AE Sewing Machines to quickly develop and visualize the cell design, effectively communicating project concepts to the customer.
Reduced Build Time
AE Sewing Machines met their 45-hour build time target using Vention’s flat-pack kit, saving 40% in setup time and avoiding additional costs.
Compact, Optimized Design
AE Sewing Machines adapted an initially large design into a sleek, compact unit that seamlessly fits into the client’s facility.
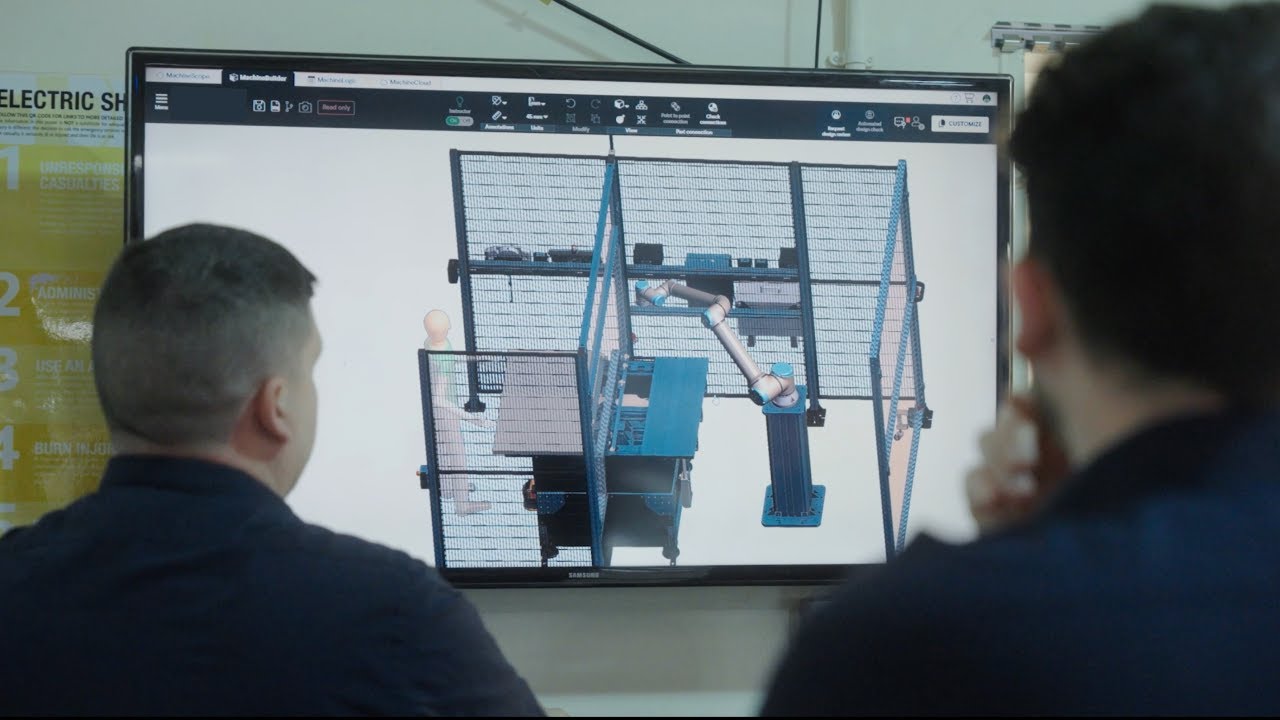
The Problem
AE Sewing Machines aimed to address key challenges facing their customers, including an aging workforce and the absence of a consistent, reliable manufacturing process.
The existing manual operations, combined with the need to standardize over 20 distinct textile applications, prompted AE Sewing Machines to pursue automation solutions designed to enhance safety and improve throughput.
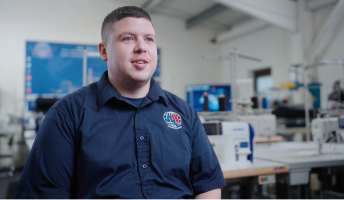
"The reason that we were so passionate to work with Vention is because they offered us a full turnkey solution, right from concept, to delivery, to integration, and then deployment."
The Project
To streamline the process, AE Sewing Machines developed an automated ultrasonic welding station for textiles. Using Vention’s MachineBuilder software and a Universal Robots UR 10 cobot, they were able to accelerate the deployment timeline.
The system enables an operator to load textiles into the station while the cobot ultrasonically welds the materials, enhancing production throughput and operator safety—all controlled through Vention’s MachineMotion plug and play PLC motion controller.
Special considerations included a compact design to fit the client’s space and addressing repetitive strain injury (RSI) risks for operators handling dull and monotonous tasks.
The Results
Partnering with Vention allowed AE Sewing Machines to bring this confidential project to life, achieving the meticulous standards and rapid timelines required for specialized tasks. The team completed the ultrasonic welding system build in less than the planned 45-hour timeframe.
In the design phase, they transformed an initially large, space-consuming concept into a compact, streamlined unit that fit seamlessly within the client’s facility, leaving room for future expansion. The project’s complexity required close collaboration between AE Sewing Machines and Vention, with visual tools and prompt feedback allowing the team to refine the concept into a practical and adaptable solution that could scale. Intimate knowledge of the textile industry and a deep commitment to customer needs drove the success of this intricate build.
The assembly crew leveraged the real-time guidance offered by Vention’s MachineBuilder platform to stay on track with their initial budget goals and timelines. They were able to deliver the entire system within six to eight weeks - a remarkable improvement over typical 12 to 24-week deployment timelines for similar projects.
Beyond technical achievements, this project highlighted AE Sewing Machines’s dedication to safety and long-term industry impact. By automating the workstation, they reduced repetitive strain injury (RSI) risks, allowing operators to remain safely outside the action zone while the robotic arm handled ultrasonic welding tasks.
With this project, AE Sewing Machines not only strengthened their role as a leader in textile automation but also underscored their dedication to evolving British manufacturing while meeting the highest standards of confidentiality and trust.
Project Specs
Learn More About the Vention Automation Partner Program
Join the VAP Program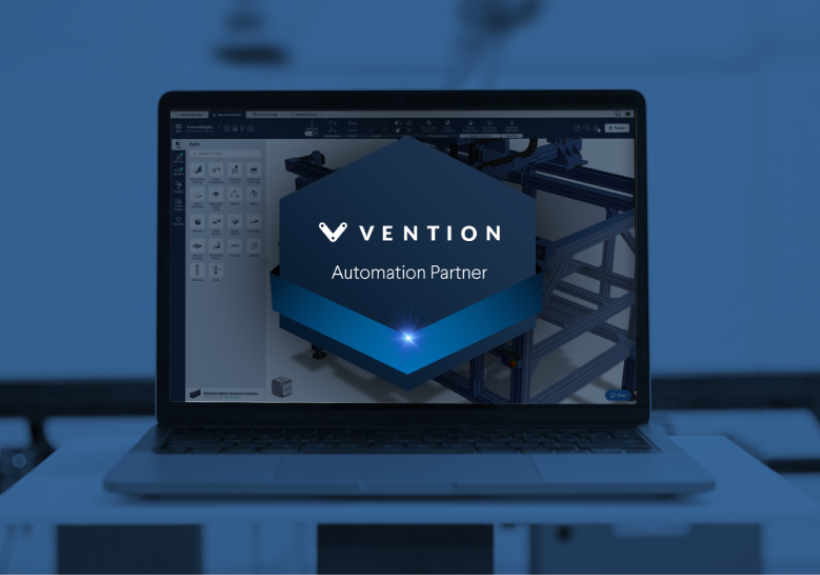